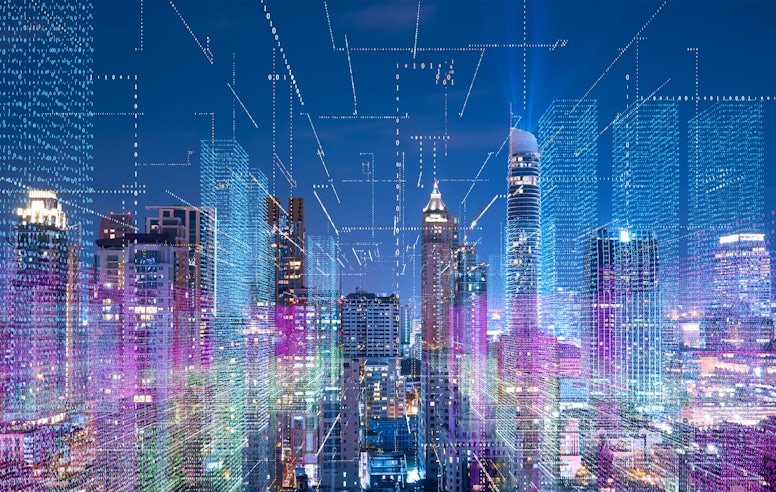
Understanding IoT in Building Automation
Commercial building automation has been around for a long time, yet serious technological advancement has struggled to take hold in the industry over the years. This is largely due to the complex needs of large building systems and the subsequently complex building automation system architectures designed to match.
As the Internet of Things (IoT) gained popularity in other industries over the last decade, however, most building controls companies started introducing IoT technology to their solutions via gateways and bolt-on connected devices. These networked devices can extend the functionality or flexibility of traditional building controls — such as incorporating indoor air quality management (IAQM) — but they don’t do much to reduce widely-felt implementation barriers such as cost and complexity.
This article seeks to define the varying ways in which building control companies use IoT today, from smart systems and smart layers all the way to native IoT Building Management Systems (BMS). It will discuss the benefits and limitations to IoT bolt-ons, and explore how building automation with a foundation in IoT can change the way we monitor and control buildings forever.
Smart Systems are Based on Traditional Automation
Honeywell is one example of a company that has excelled at the transition from traditional building-block automation to adopting forms of modern technology by launching smart, internet-connected product lines alongside a proven portfolio of legacy wired sensors, thermostats, and controls to modernize their offering. Their integrated building management system— sometimes called an iBMS —is similar to popular solutions offered by Carrier, Johnson Controls, Schneider Electric, and others, but they all have several obvious and inherent disadvantages for most commercial buildings.
The most common complaint is the cost and complexity of these amalgamated solutions. In addition to the expense and labor-intensive programming required to build out proper building control sequences, and purchase and manage the licenses and upgrades required for subsystems to remain compatible, there are the additional challenges of incorporating exponentially more IoT-based data or additional points into those systems. Much has been written about the limitations of these existing automation and control platforms to supervise, manage, adjust, or deploy properly.
This introduces a second limitation, which is proper commissioning. Commissioning is a systematic process conducted after the installation or upgrade of HVAC equipment or controls to verify that an HVAC system meets the designer's intent and specifications. Upgrading buildings with an array of IoT sensors and controls to existing HVAC controls systems without retroactively recommissioning those systems often results in conflicting or corrupted data, increased maintenance and equipment cost, reduced comfort and energy efficiency, and diminishing building performance.
What are Smart Layers, and Why do we Use Them?
Smart layers sit on top of an existing building automation system and often come from third-party companies. Building operators may choose to add these layers for a few different reasons — adding cloud connectivity, for example, or purchasing a sensor overlay for more detailed IAQM.
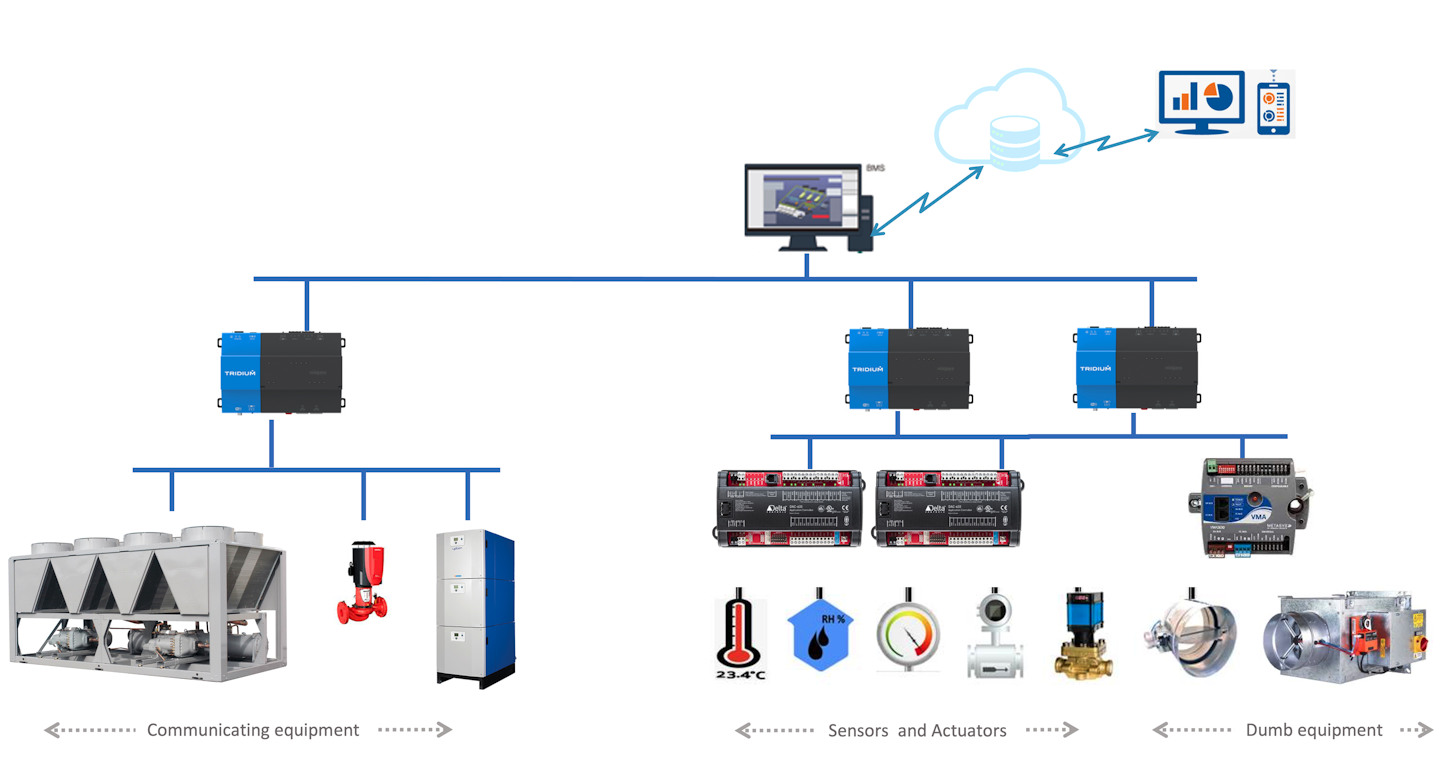
Including cloud connectivity as a new layer in offline automation systems was among the first attempts at utilizing IoT in building automation. It allows building data to live in the cloud rather than strictly onsite, giving building operators the ability to view their data remotely.
While this approach is more advantageous than systems with data available only through an onsite supervisor, its potential for growth beyond this is limited. The data streaming from these antiquated systems are not typically properly tagged or defined, making them difficult to interpret and integrate. And in these scenarios, cloud connectivity mostly only works in one direction — data can stream up to the cloud, but control commands cannot be sent down remotely.
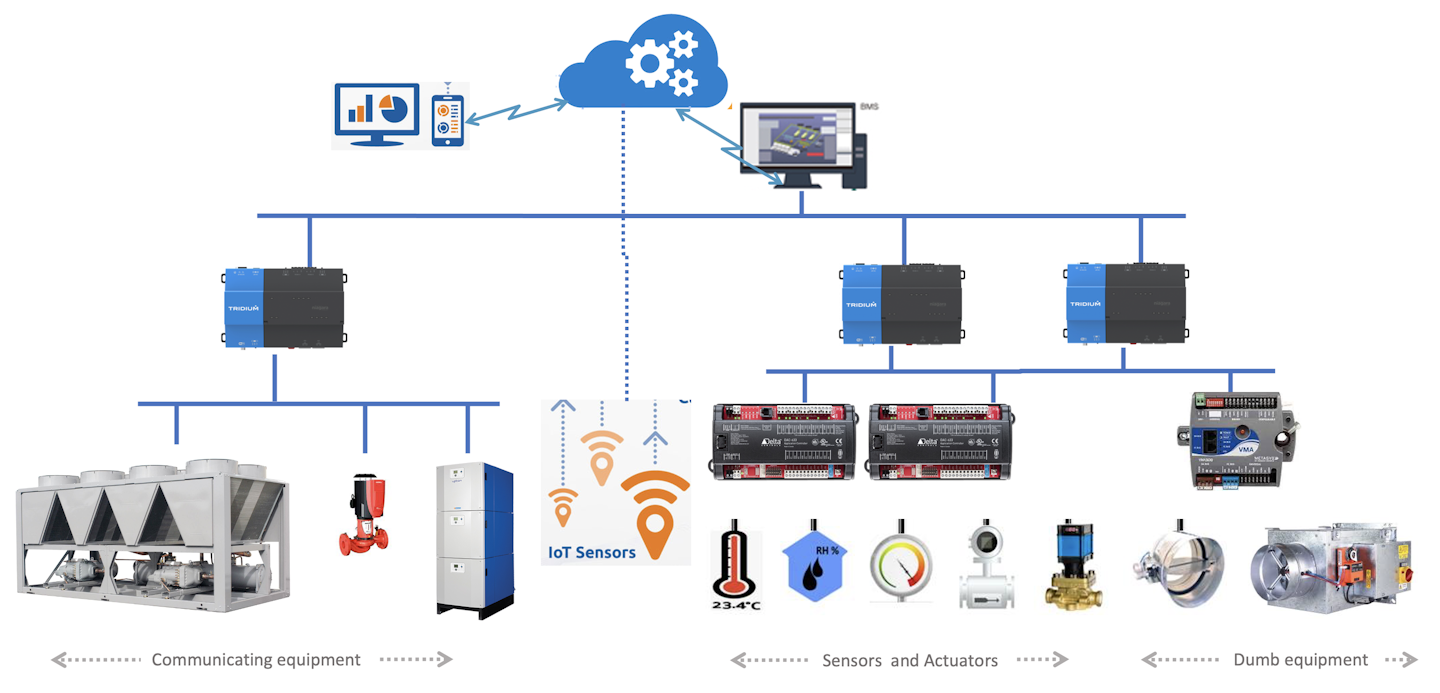
Connected IAQ sensor overlays present a similar problem. When installed on top of an existing building automation system, sensor overlays can widely extend a building operator’s ability to see air quality data such as volatile organic compounds (VOCs) from their spaces and make better-informed decisions. That’s the catch, though — data from these overlays are for monitoring only, meaning facility managers still must make adjustments manually within the foundational automation system. The sensor overlay data does not feed into any control sequences that adjust automatically and over the air, creating yet another information silo that is blind to the systems around it.
For a building automation system to be cloud connected in both directions and provide centralized, holistic insight and control, it must completely diverge from traditional automation architectures, their custom programming requirements and on-site supervisors, as well as today’s IoT layering attempts. The future of automation lies with systems that are built on IoT from the beginning.
IoT-Based Building Management Systems are a Fundamental Shift in Automation Architecture
Rather than adding a series of architectural layers or new devices to a system, a true IoT-based BMS elegantly collapses its architecture and incorporates IoT from the ground up. The result is a BMS that can holistically monitor and optimize building performance for energy efficiency, comfort, and IAQ at drastically reduced price and complexity thresholds, changing the game for an industry historically tailored to large commercial buildings.
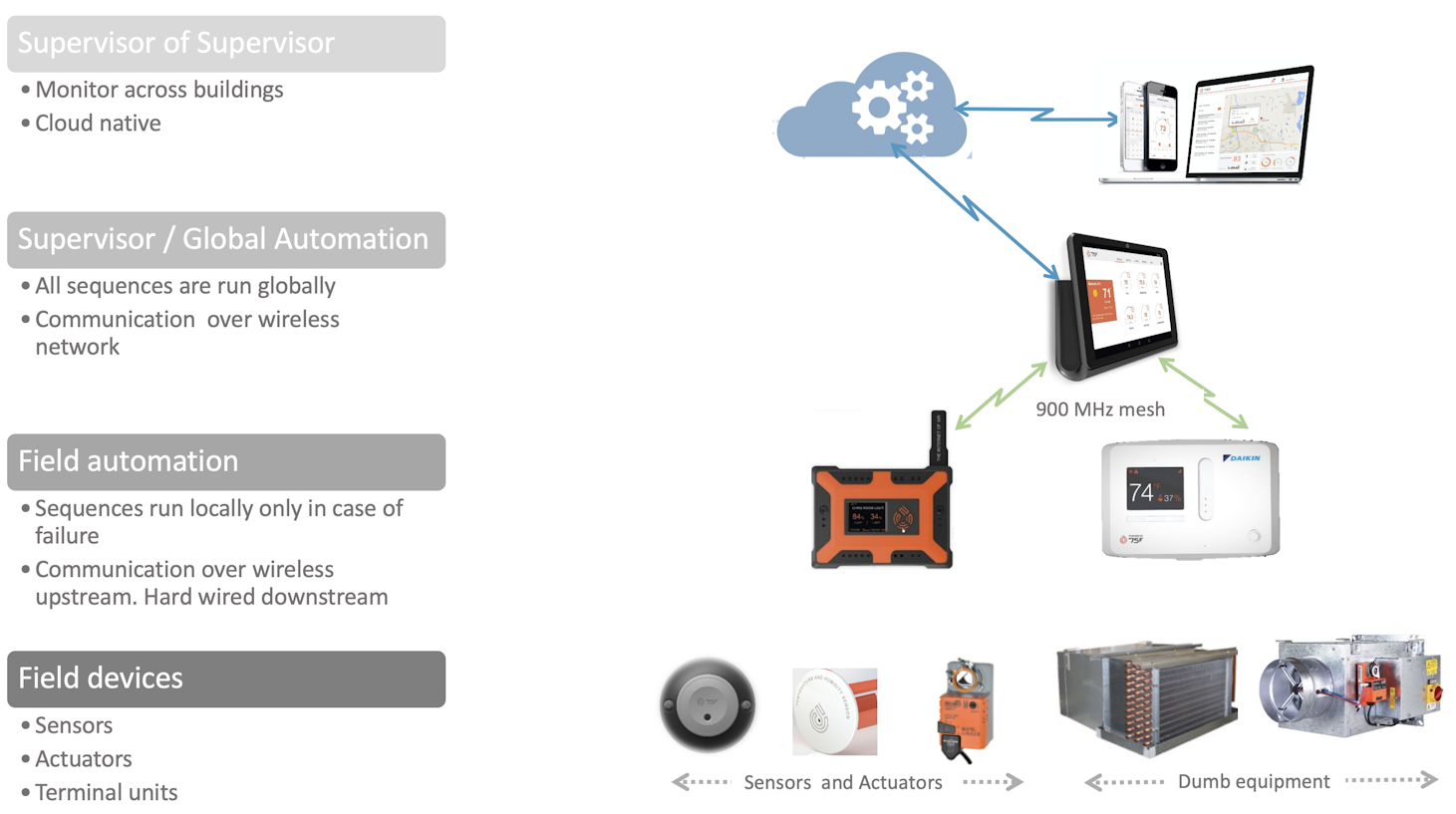
In an IoT-based BMS, data inputs from sensors, equipment, and occupants move wirelessly through an onsite gateway to the cloud, where built-in sequences tailored to the building’s equipment then make informed control decisions. These decisions travel down back to the building in the form of output decisions or micro adjustments seamlessly. In this scenario, networking and integration are eliminated, and all commissioning occurs continuously. Because the system is based in the cloud, both monitoring and updates can be carried out remotely.
Data that streams from an IoT-native system is clean from the ground up, as well, providing vast amounts of clear, readable and actionable data from our commercial buildings for the first time. This powerful dataset can automatically inform the digital twin and gives building operators unprecedented access to data analytics that can be easily understood and securely shared with internal and external parties. With automatic and industry-standard tagging, the opportunity for integration is endless.
This simplified approach to building automation unlocks sophisticated technology in the mid-sized commercial building market by reducing installation time, system complexity, and total project costs.